Our epilamization agents comprise a carrier fluid (solvent), the active ingredients that act on the surface and various added ingredients whose function is to improve the solvent's wetting properties. The epilam coating can be applied to components by immersing, spraying or printing them. The actual process of creating the coating takes place when the solvent evaporates. The active ingredients which form the boundary coating polymerize on the surface of the solid body and form net-like structures on the fluoractive tensides with individual polar molecules standing vertically.
Immersion time can be very short (seconds). A spray map can help when spraying bearings. Components can be stamped with felt stamps. Application by brush requires considerable experience because it is hard to see areas that the epilame coating has missed.
Epilamization procedure:
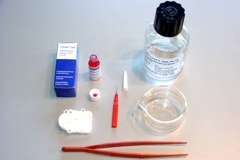
Test oil with plastic cap, oil stic, tweezers, glass dish and Antispread
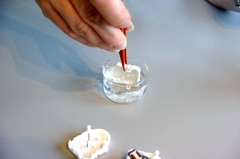
Immerse component (approx. 2 secs.) then allow to dry (10 secs to 2 mins. for concave surfaces)
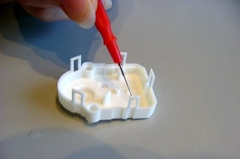
Apply drop of test fluid - 24 hours later there must still be no visible wetting.
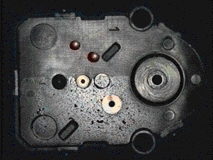
Upper half epilamized - fixed. Lower half not epilamized - fluid has spread out completely.
Problems that may occur when forming the coating
The bonding of the coating is affected by the cleanliness of the material surface. Any particles left behind after machining processes, and especially hydrocarbons and tensides, reduce the adhesive strength of the epilam coating. Any processes which affect the boundary layers, e.g. smoothing of fibreglass surfaces in order to strengthen polymer materials, prevent the formation of an adequate epilam coating on fibre reinforced plastics.
Examination epilamization
Since epilam coatings can be less than 0.1 mm thick, the only way to check them is with a procedure that compares surface wetting. For this purpose a test fluid with a known and - most importantly - very low surface tension is applied to the epilamized surfaces. When a surface has been epilamized adequately and correctly, small (approx. 1 mm) droplets of lubricant will form smooth-edged semi-spheres. The same droplets of lubricant on a non-epilamized surface will spread within a few minutes and form patches of around 1 cm² in size.