Danger of wetting with long-term effects
Epilamization can enable reliable functioning over many years, even with lubricants with a strong tendency to spread. On rough metal and plastic surfaces, where operating temperatures are high or changes in temperature are sudden, epilamization can significantly improve functional reliablity.
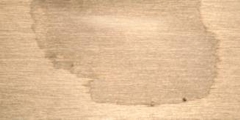
Solid body's surface winning. Total wetting.
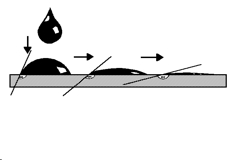
Surfaces want to be wetted. "Formation of a grease spot".
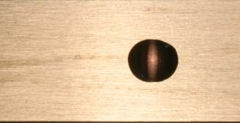
Oil drop winning. No wetting.
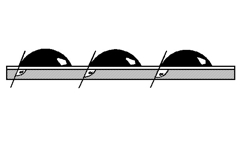
Drops have stable wetting angles due to epilamization.
Spreading occurs when the surface tension of the solid body is greater than that of the fluid.
Danger from long-term effects
It may take years for the fluid to wet the entire surface or to reach critical components. It has been known for spreading to occur over 100 cm or more!
Physical/chemical reactions due to wetting (contamination)
Creeping lubricants reach areas of the componentry where they can cause dangerous changes. Such changes can occur in materials or electrical components. When lubricants come into contact with incompatible materials, physical/chemical interactions may ensue. For instance, if thermoplasts are used with amorphous materials, stress cracks may develop. In this case even minute quantities (a film) of creeping lubricant can initiate the process of stress crack formation. At points where there are significant differences in wall thickness or where stresses are built into a component as a result of injection moulding processes, components will develop surface cracks which may progress to the point at which parts of the assembly groups such as snap connectors or PCB supports, will break off. This process has not yet been fully explained. The effects on materials described above represent the worst-case scenarios and the most dangerous situations; there can also be less serious problems where materials, seals, paints, adhesives etc. swell, become soft or brittle. However, such problems only occur with considerably greater quantities of creeping oils.
Electrical problems caused by wetting (contact damage)
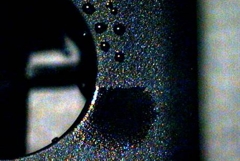
Contact surface (left), upper half of PCB epilamized. Lower half not epilamized. Wetting on contact surface.
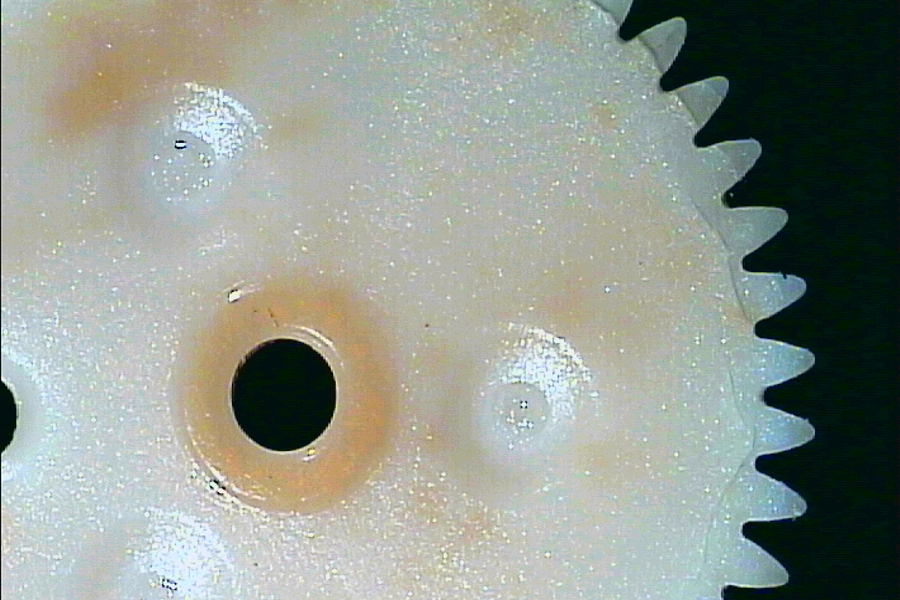
Gear wheel with cracks around the teeth
There are several ways in which electrical components can become damaged. One of these is the direct effect on electrical contacts (e.g. the collector in small motors, relay contacts, potentiometer circuits, etc.) by the lubricant's property of being an ideal insulator. In these cases the transfer resistance of electrically charged components is increased. If arcing occurs, the lubricant that has been drawn up is broken down and reaction products are formed, in some cases with catastrophic results. Such reaction products can be especially critical in the case of silicone oils, as the products formed by their breakdown create glass-like coatings in the microscopic contact area. Above all, people are wary of using products containing silicone because even small portions can be transferred onto surfaces via the vapour phase. The condensing microparticles then also (and often invisibly) wet the surfaces.
Faults in potentiometers and wipers caused by wetting (malfunctions)
In potentiometer circuits with a highly-complex layer structure, the film of lubricant in combination with wear processes causes serious problems. All potentiometer circuits and the associated wipers are designed in such a way that a certain degree of wear is desirable; components are designed with this in mind. This wear results in a specific cleanliness of the sliding components, and therefore constant contact resistances. The small particles created through wear are brushed away by the slider out of the actual wear zone. In the case of the wetted surface of the piste, however, the worn piste material is turned into a paste with the film of lubricant. The particles are no longer loose and isolated but combine to form larger units which can be so disruptive that they lift up the wiper fingers from the piste material. This effect can result in an unforeseen complete failure of the system. In modules with a safety implication, e.g. electronic control elements in motor vehicles, this effect can result in highly dangerous malfunctions.
The effect of the epilam coating on contact resistance
The epilam coating is always thinner than the peaks in the surface roughness. There is no measurable increase in contact resistance. Sensitive plug connectors can now be successfully epilamized. By epilamizing plug connectors, FLUX can also be prevented from penetrating them.
SIF (surface infecting fluid) is a term that has been coined in Britain and America, and it refers to the infection of surfaces by unwanted fluids; this can be considerably reduced by epilamizing the components. The epilamization agents used today are safe, and can be used with a majority of materials. This method is used with many components in the automotive industry, where it is regarded as state of the art.